Students in the McKelvey School of Engineering at Washington University in St. Louis designed prototypes for a device that could help environmental engineers monitor the air quality impact of factory farms in Missouri. The students built their prototypes in the Spartan Light Metal Products Makerspace in Jubel Hall over the course of the fall 2023 semester.
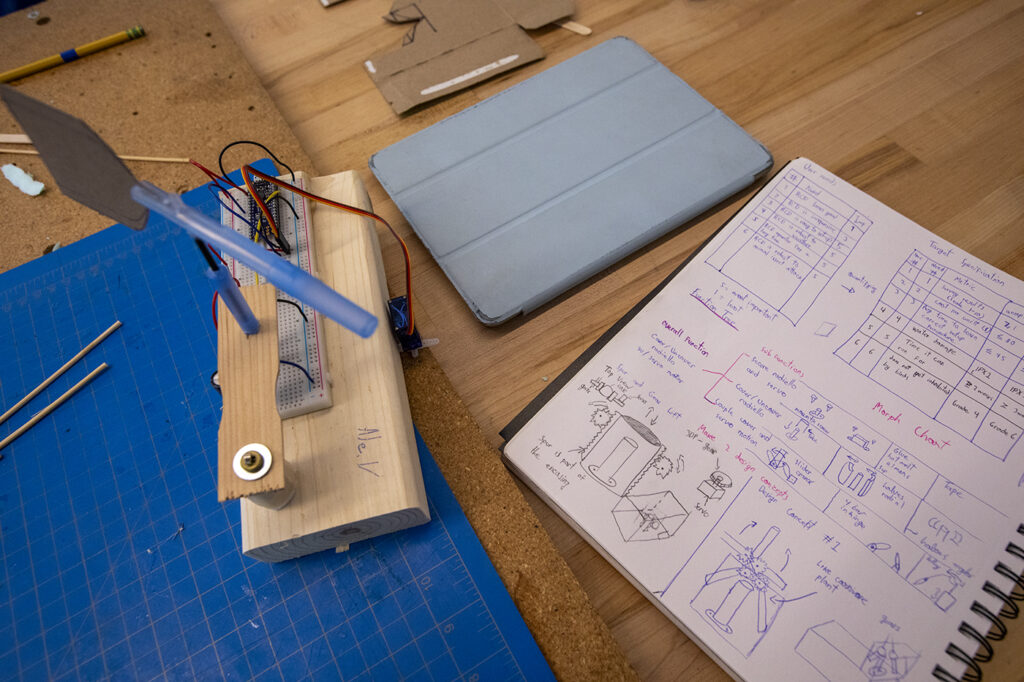
Working with lecturer Jackson Potter, undergraduate students in the upper-level “Multidisciplinary Design & Prototyping” class (MEMS 312) developed their prototypes to meet a need described by environmental engineers in Jay Turner’s research group. Turner is the James McKelvey Professor of Engineering Education.
While much of the nation’s animal agriculture production once occurred in open fields, today most animals raised for human consumption live in Concentrated Animal Feeding Operations, or CAFOs. If not designed or managed properly, these intensive farming operations can pollute local air and water. People who live or work near CAFOs, especially those who spend a lot of time downwind of them, experience the brunt of the negative impacts.
“Basically it stinks — in one direction,” said Celine Vuong, an undergraduate student who developed one of the prototypes, along with her class partner, Jaimie Lin.
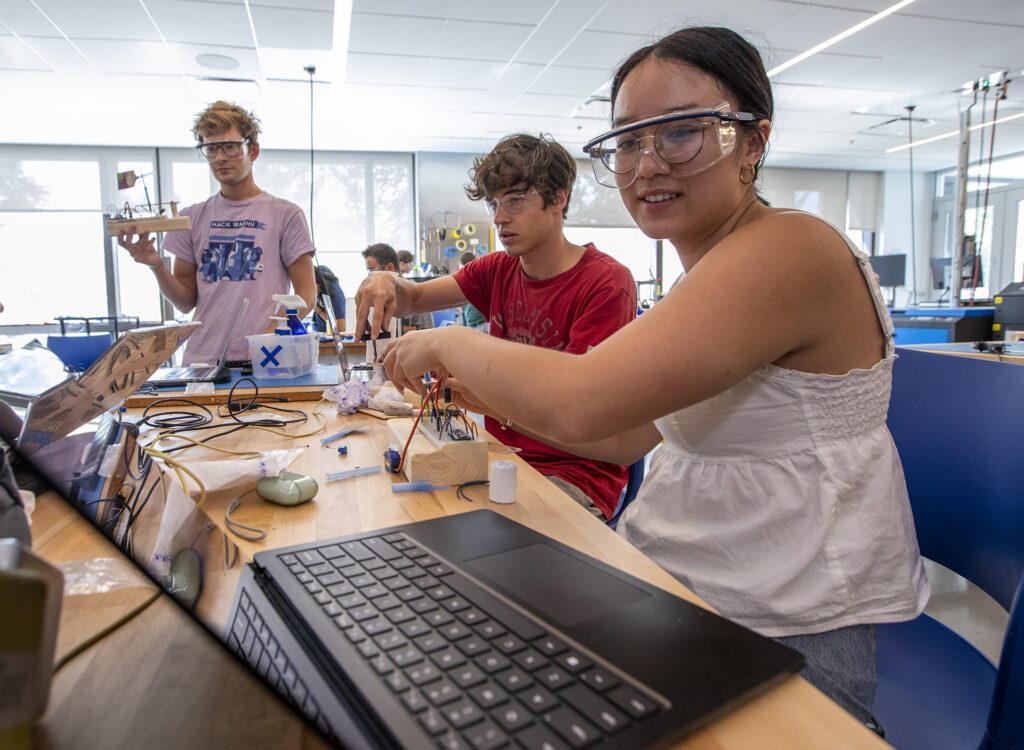
In September, Potter invited the Turner group researchers to visit his class and describe the simple and low-cost air quality monitoring devices they are installing at properties adjacent to CAFOs. The scientists needed a way to shield their sensitive sampling equipment until the wind picks up in the “right” — or, depending on your perspective, “wrong” — direction, ie, from the farm. The researchers wanted their sensors to remain open, or exposed, while the wind blows directly from the farm, and cover the sensors when the wind shifts to a different direction.
Over the fall semester, the students grappled with many decisions related to their prototypes: Is it better to 3D-print something, or to export a 2D pattern and have a machine cut the needed part out of an existing pane of plastic? Which solution is going to be airtight? How many batteries are needed to operate the mechanism? And, at a practical level, what happens when the 3D printing queue at the makerspace gets too long?
Ultimately, the students pictured their internal customers as they made their final design choices. “You want to make it easy for the people who will install it,” Vuong said. “There’s lots of things to consider.”
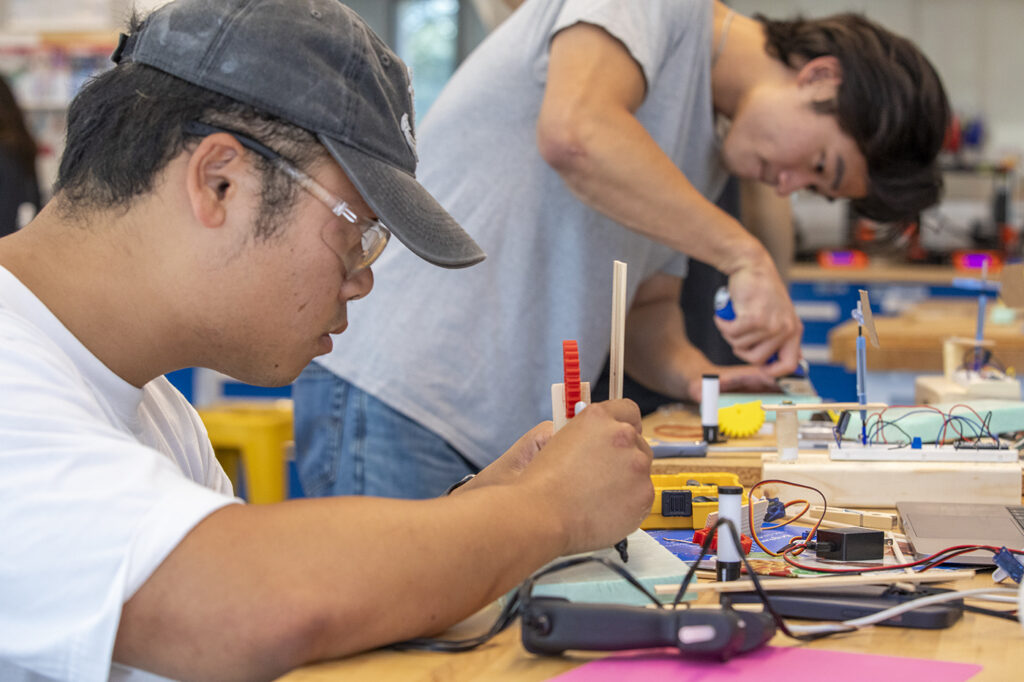
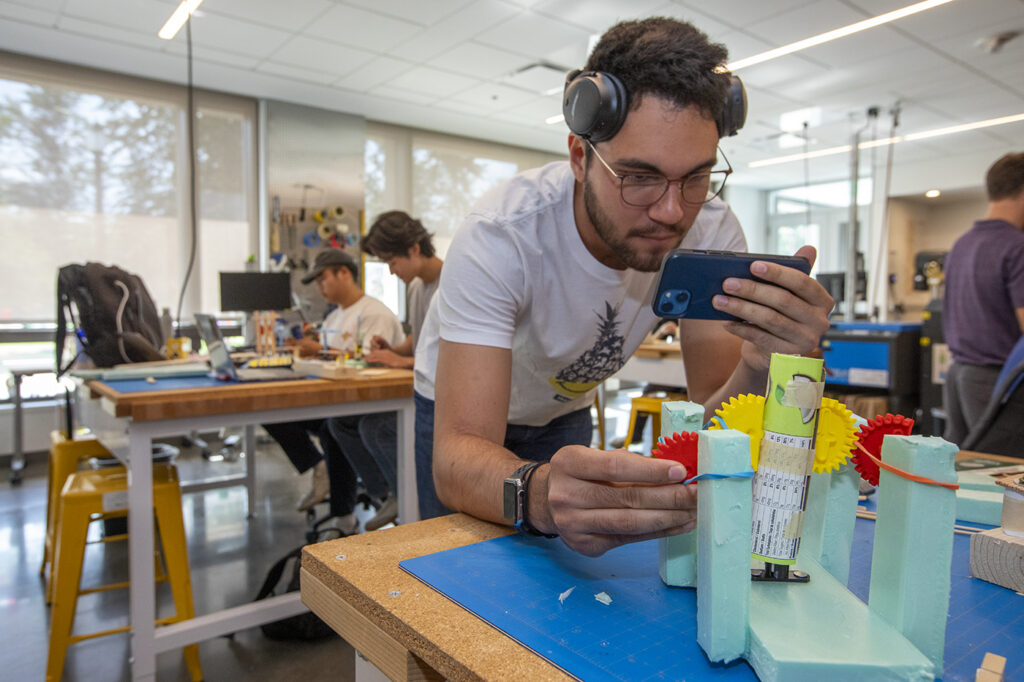
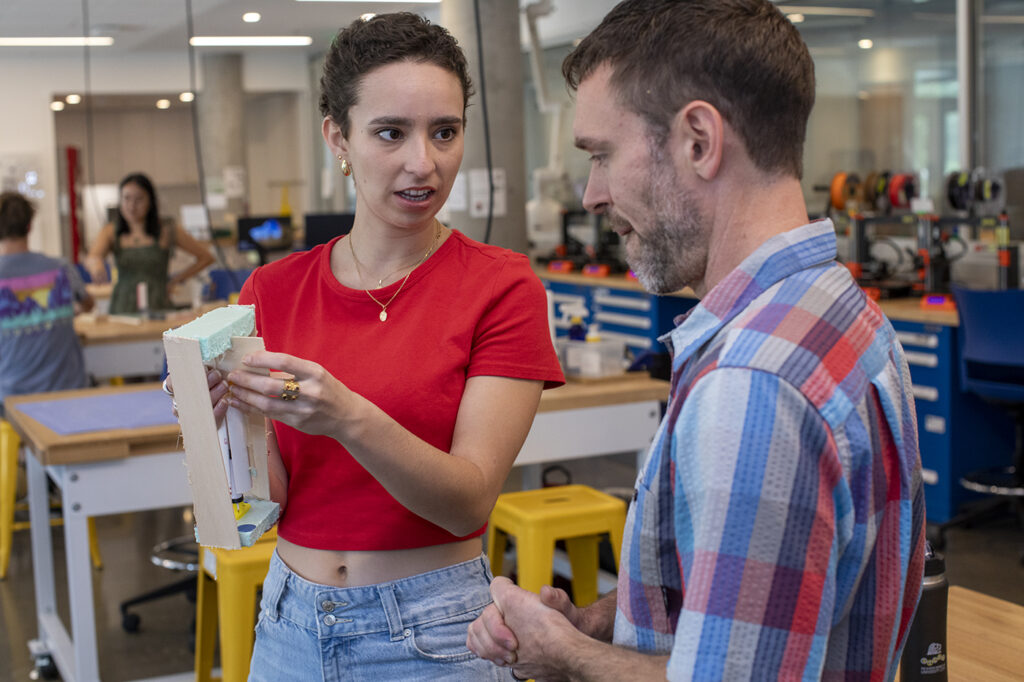
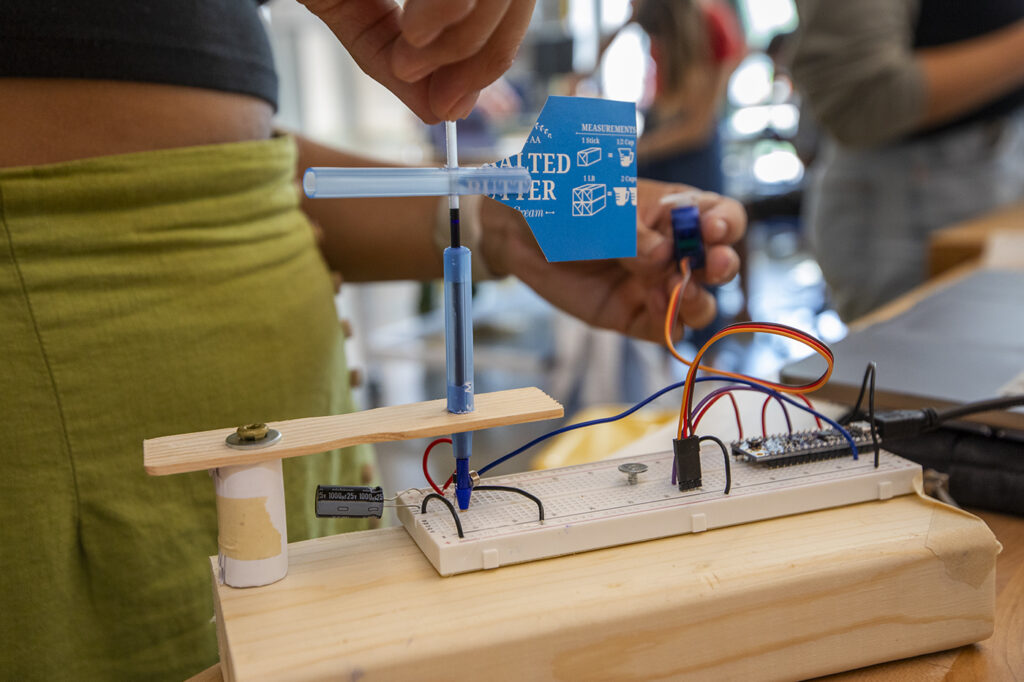
Undergraduate student Matthew Ren said his design was inspired by a revolving door. His prototype featured a small 3D-printed cylinder that fits like a sheath over the sensor. A curved panel slides open when the wind picks up from a particular direction to reveal the sensor.
“The target user might not have a lot of experience or knowledge in mechanical engineering or electrical engineering,” Ren said. “I want them to feel very confident and empowered. Everyone can use this device. They can replace the sensor or the motor if it’s broken.”
The students displayed their final projects for the public at a showcase event at the Danforth University Center (DUC) on Dec. 5.
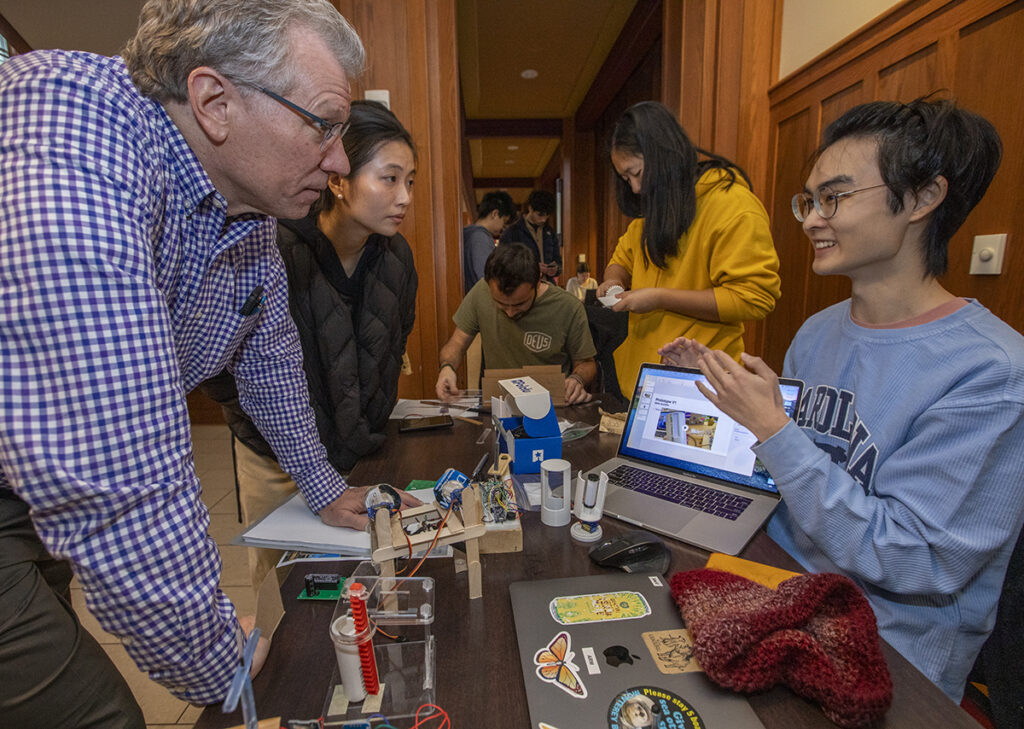
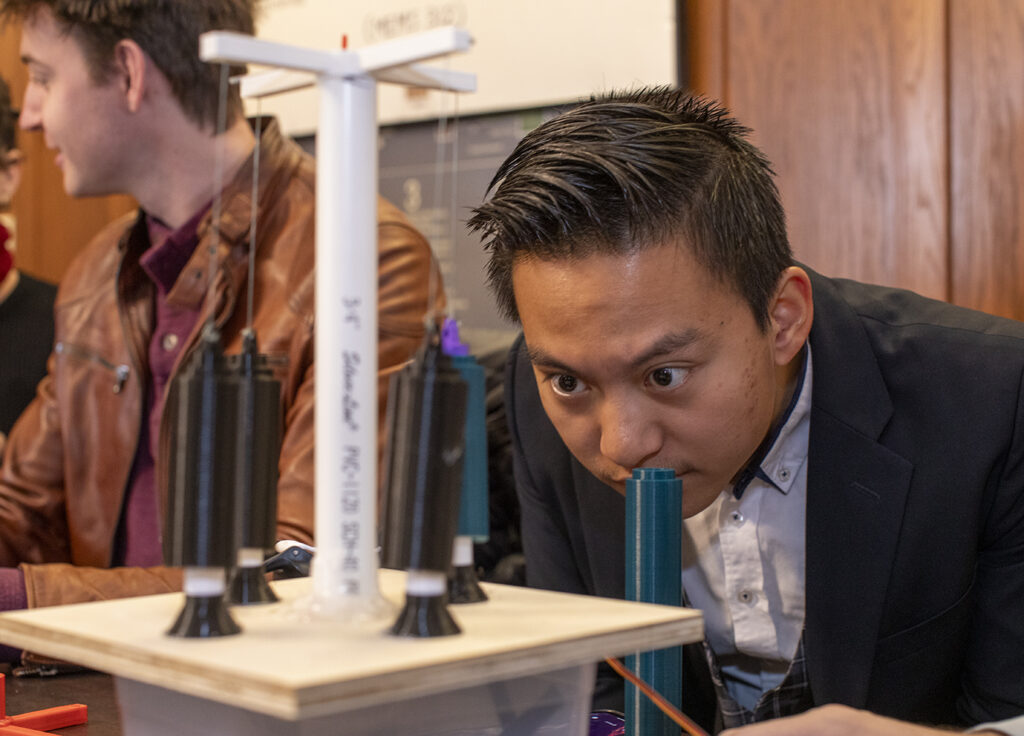
Yizhe Zhang checks the cables in his prototype design during the Mechanical Engineering & Materials Science Prototype Expo.
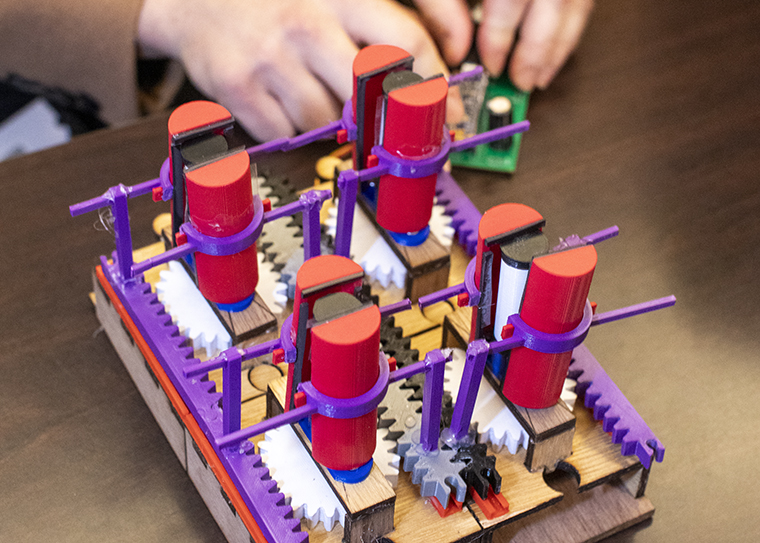
“Everything here is so diverse! It’s totally different from what I thought before this class started,” said Yan He, a doctoral candidate in energy, environmental and chemical engineering at McKelvey. She is leading the Turner group collaboration with the Missouri Coalition for the Environment on the project related to local CAFOs.
“Many of the devices are simple, and they’re working properly,” she said. “In the future, we’re going to deploy some of them in the field.”
“There’s elegance in simplicity,” said Turner, who was smiling broadly as he made his way from one crowded table at the DUC to the next. “There are a few things that we are always fighting in the field: Is it watertight? And what has the fewest number of moving parts? I love the ideas we see here.
“There’s one that has a magnet that holds everything tight,” he said. “When you want to open it, you have to overcome the force of the magnet to get it apart. You’re actively working to create a seal.” He also complimented designs that relied on gear mechanisms and a rotor turning a rod to open and close. “There’s nothing complicated about it,” Turner said.
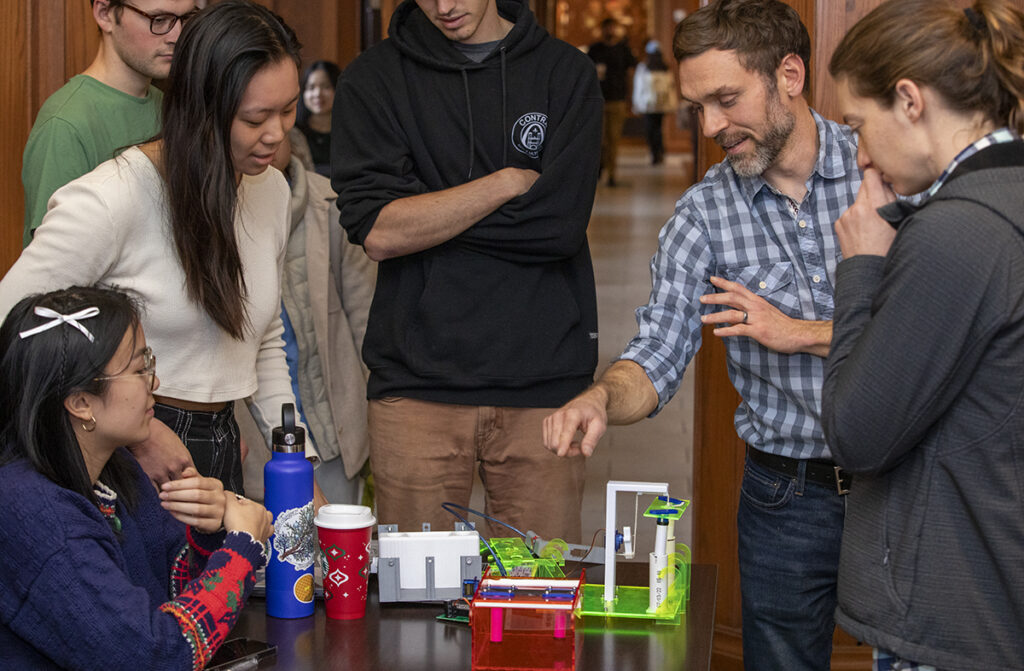
Potter, who teaches both the MEMS 312 class and MEMS 411, “Mechanical Engineering Design Project” (“Senior Design”), asks his students to reflect on their mistakes and missteps when they present their prototypes to their peers. It’s a required part of class.
“If you’ve seen more things that can go wrong, you’ll be better able to avoid doing those things yourself (usually),” Potter said.
“Students also get a more realistic picture of the design process,” he said. “Needing to rethink or rework is an inherent part of making something new.”
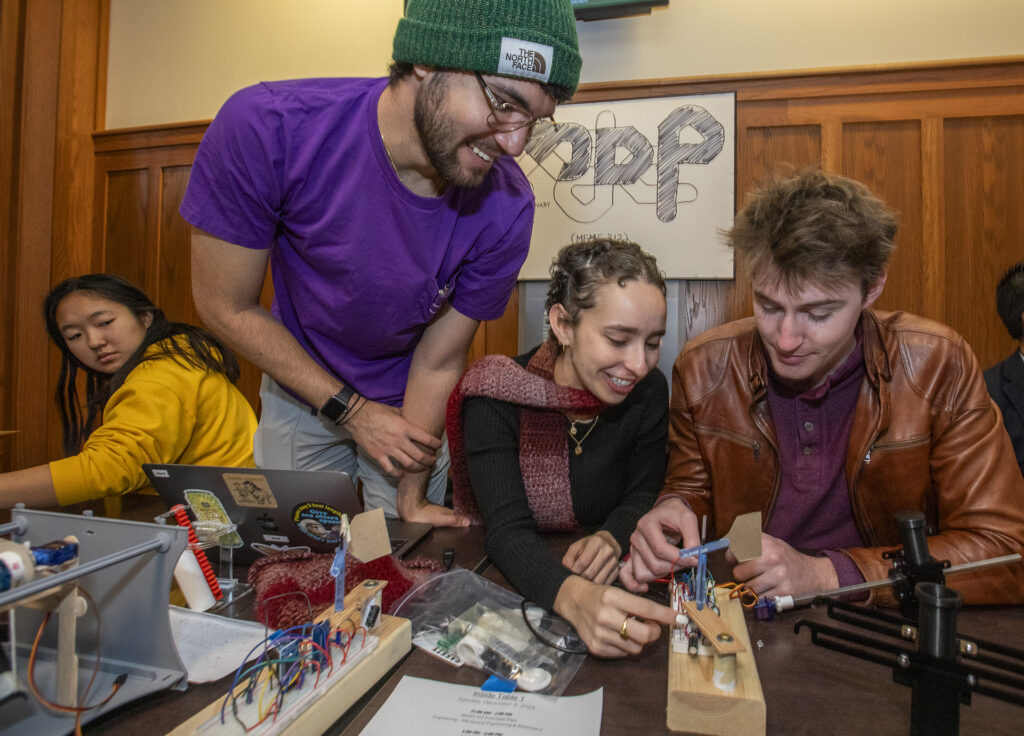