Because of the worldwide havoc caused by coronavirus, supply chains have become a crucial new focus of the global economy. Along with health care providers, workers in logistics and transportation have emerged among the people essential to sustaining life through the pandemic.
As a result, a Washington University in St. Louis expert foresees permanent changes ahead to guard against massive stresses on supply chains and better ensure their workers’ safety.
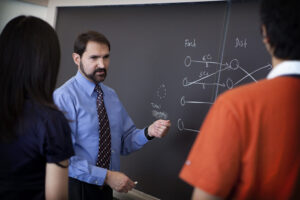
For starters, Sergio Chayet, director of the Operations and Supply Chain Management MBA platform at Olin Business School, expects sweeping change around how companies model and mitigate future risks to their supply chains.
“In supply chain risk management, planners start by identifying and assessing possible risks, which are classified according to their probability and anticipated impact. These are called foreseeable risks and are managed proactively,” said Chayet, a senior lecturer in operations and manufacturing management.
“Relatively likely risks should be mitigated by measures designed to lower their probability or impact before they happen,” Chayet continued. “Because of limited resources, less likely risks are best managed by contingency measures, which are planned ahead but only triggered after the risk happens. Remaining risks are called residual or ‘unknown unknowns’ and can only be managed reactively. The only proactive measures for those are setting aside time, resources and flexibility to be used once the risks are known.”
When major unknown-unknown risks were modeled in the past, Chayet said they were usually assumed to happen one at a time and independent of each other. However, COVID-19 turned out to be an unprecedented set of unknown unknowns all happening in rapid succession — lockdowns, factory shutdowns, economic collapse. The result was an unprecedented upheaval in global supply chains.
“In the future, a global pandemic of this magnitude will not only be a foreseeable event, but also will likely change how we model unknown unknowns,” Chayet said. “And depending on how likely similar pandemics are expected to be in the future, a whole slew of mitigation and contingency measures are likely to be considered.”
What went wrong?
Perhaps the most alarming supply chain failure was the lack of face masks, gloves, hand sanitizer and cleaners needed to keep health care providers and other essential workers safe. What went wrong?
“Part of the risks were foreseeable and part were unknown unknowns. We had the H1N1 (swine flu) pandemic in 2009, so the risk should have been foreseeable for federal, state and local agencies,” Chayet said. “I’m not sure we have all the details about the humanitarian response of those supply chains, but once those come to light, it would be important to figure out if the risks were ignored, the initial contingency plans were inadequate or the plans were adequate but poorly executed.”
Supply chains dealing with a few products were hit especially hard by hoarding and panic purchases, Chayet said. Most food supply chains have been able to bounce back quickly and, within a few weeks, shelves in grocery stores started to look less empty. This seems to have calmed down consumers into curtailing panic purchases, he said.
Other supply chains have not been able to recover as quickly.
“Take toilet paper: Because it’s a commodity, manufacturers have little influence on market prices. To be competitive, they must control costs and usually rely on high levels of automation, low levels of labor and high-capacity utilization, with plants running 365/24/7.
“Such an unpredictable spike in demand — likely driven by a vicious cycle of panic purchases and perhaps some speculators planning to make quick profits in secondary markets — quickly depleted most of the channel’s inventory. With no excess capacity, we can expect a lag until those products are back on the shelves, which will probably be followed by more panic purchases and secondary spikes.”
Amid the lockdown, consumer demand increased because people weren’t tapping into supplies at work, schools, restaurants and so on. Unfortunately, commercial toilet paper cannot easily be repurposed for consumer use because the rolls do not fit on residential toilet paper holders.
“This has further strained consumer supply chains and will further delay the time it takes for manufacturers, distributors, wholesalers and retailers to replenish inventory to the new necessary levels,” Chayet said.
Protecting workers
Looking ahead, he said that many of the measures that have been put into place to protect companies’ greatest assets — their workers — will likely continue.
“Some of the changes in grocery stores, such as plexiglass protection for cashiers, changing the flow of customers within stores, etc., may become permanent,” he said. “New technologies to limit transmission of airborne infections, such as new HVAC filtering systems and more intense UV disinfection protocols, could arise.”
Other standard operational changes Chayet expects to see as a result of COVID-19 include investments in personal protective equipment for service workers and training on how to use them across different industries, as well as more robust resources and contingency plans for virtual work.
WashU Response to COVID-19
Visit coronavirus.wustl.edu for the latest information about WashU updates and policies. See all stories related to COVID-19.