Communities around the world are increasingly using a process called reverse osmosis (RO) to produce drinkable water. It’s estimated that more than a billion people could be consuming RO water by 2050. But much of value is lost in that process, a fact that drives the research of Young-Shin Jun, professor of energy, environmental and chemical engineering in the McKelvey School of Engineering.
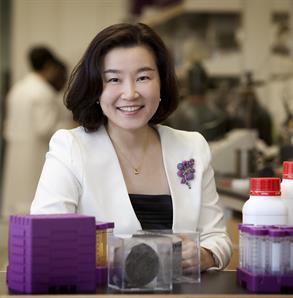
From Jun’s perspective, wastewater in the environment is not just H2O molecules. “Water always occurs together with a very useful bag of materials,” she says. That bag could contain calcium carbonate, magnesium hydroxide, sodium chloride, potassium chloride, lithium, and numbers of other reusable (and scarce) chemicals for industry and agriculture.
All are useful materials. Now, with a $1.35 million grant from the U.S. Department of Energy, Jun and her colleagues are working to open that bag and let those materials out.
“It’s not a treatment process; it’s a production process for both clean water and valuable salts,” she says about working with the leftover waste from RO, called reverse osmosis concentrate (ROC). Jun and her project team will develop a coupled process of electrochemical treatment and selective solid nucleation to reuse that concentrate in new forms.
In reverse osmosis, water goes through a semi-permeable membrane, separating the clean water from its aqueous ion contents. Because mineral scales formed during the RO process can increase energy consumption and foul the membrane, RO water is pretreated with antiscalants. The antiscalants protect the membrane, but they will continue interfering with the nucleation and solidification of these mineral scales even after the RO process.
The leftover ROC compounds are converted to mixed waste solids via other processes, including brine concentration and crystallization. To harvest useful resources and to reduce energy costs, Jun will develop a method that both breaks down the antiscalants in ROC and enables the selective nucleation and crystallization of sought-after minerals and salts. So far, her lab’s research has found ways to greatly speed up this valorization and use less energy.
Treating and disposing of highly saline ROC water is expensive and environmentally challenging, and the newly developed process could greatly reduce the energy and operation costs for producing drinkable water while also recovering useful resources. The same process can also be used for “produced” water, the brine waste from oil and gas recovery.
The year 2021 saw production of some 25 billion barrels of produced water in the U.S., according to the Groundwater Protection Council. Some of that goes into the ground for reuse in fracking, but Jun’s process aims to also extract valuable resources. Instead of thinking about waste as a burden to be disposed of, Jun and her project team are embracing a “circular economy,” seeing waste as an untapped resource.
The work is a multidisciplinary project with multi-institutional teams that creates a “beautiful marriage between the chemistry and engineering processes,” she adds, noting that it couldn’t come at a more critical time as climate change ramps up. “We need to save water and energy while we remove CO2,” she says.
The process of solidifying the useful chemicals in these brines also can lock CO2 into a solid form, and then the new solid can be used for green building construction and as a useful chemical feedstock. “We aim to turn waste into a precious ore,” Jun says.